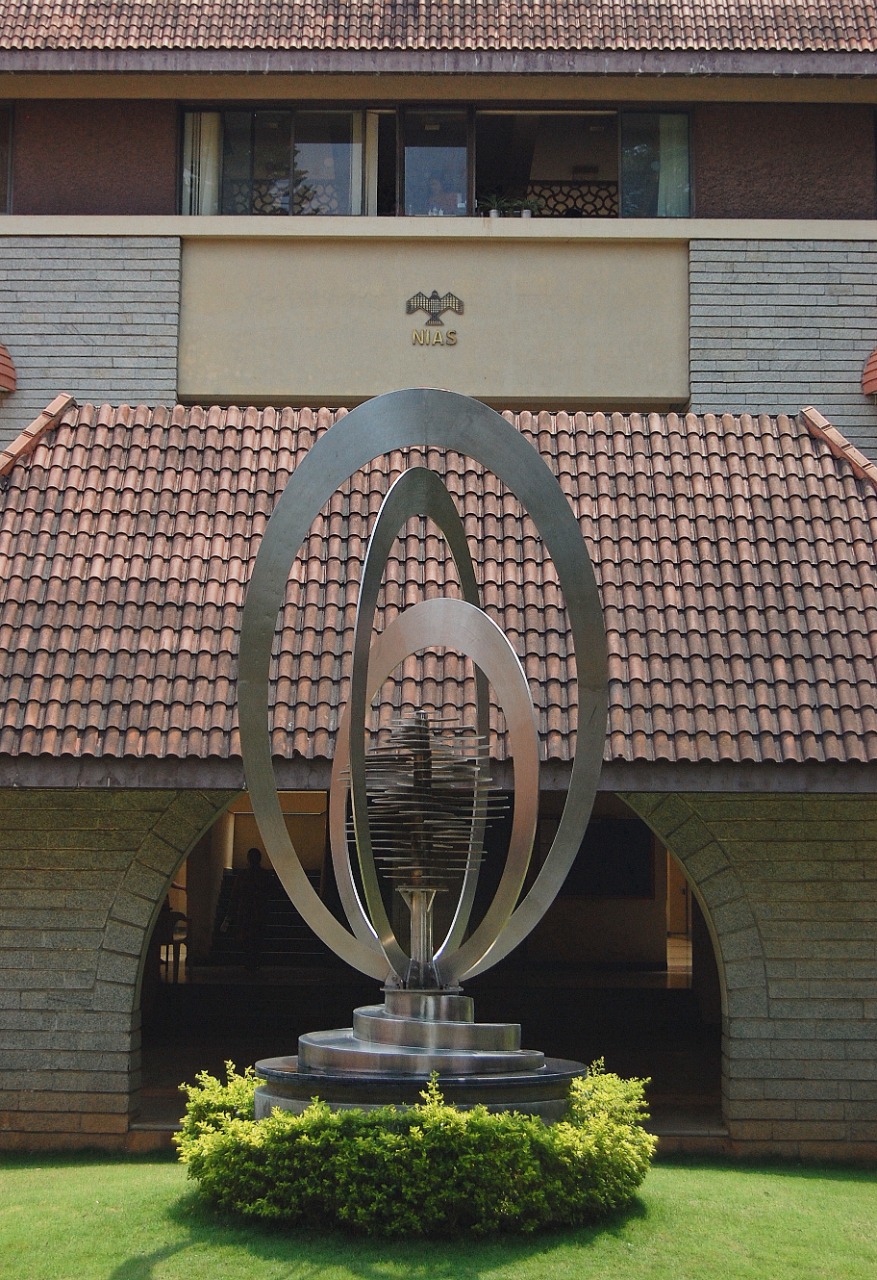
Rare earth elements are integrated into multiple industries that contribute to a nation’s economy and security. Some of these elements are considered as strategic minerals because of their use in defense, energy and various industries. The rate at which we consume these minerals is not sustainable, bringing about the necessity to develop a national strategy to extract, use and trade these elements.
Despite having reasonably large resources in the country, historically India does not have a place in the global rare earth industry eco system.
As of 2017, China has 36.6% of world resources, followed by Vietnam which has 18.3% of resources while India holds about 6% of the world’s rare earth reserves. India however produces less than 2% of the total Rare Earth (RE)Oxide produced globally. This disparity highlights an underutilization of resources and at the same time, merely selling the oxides might not be the best strategy across all the rare earth elements.
In India, certain REs are present in much larger quantities than others. These are Lanthanum, Cerium, Praseodymium, Neodymium, Samarium, Gadolinium, Yttrium and Dysprosium. The economic and strategic exploitation of these resources comes from downstream products as these are more valuable and useful. It therefore makes more sense in valorizing these elements and build an eco-system around it. How well is India using its RE resources and valorizing it?
Over the years India’s efforts have grown noticeably from being engaged in purely mining efforts to setting up facilities that can separate high purity rare earth elements. These changes span decades from the 1950’s to 2012. The setting up of separation plants PRYNCE and HERO by Indian Rare Earth Limited (IREL) allowed the separation of almost all rare earth elements, however, not all of these elements were commercialized. India’s production of rare earth carbonates and oxalates (that can be converted to oxides) are the preliminary products from separation, without undergoing any further processing or valorization. These are low-margin products that can be valorized. The major intermediates that are created from further processing include alloys, garnets, cermets and other specialized compounds.
Permanent magnets – Global Scene
Permanent magnets find use in close to every industry, from industrial and consumer electronics to automotive, medical and aerospace. The growth of both the automobile and electronics industries pushed up the demand for permanent magnets. Generating energy from wind turbines again requires permanent magnets and the current push for clean energy is again contributing to the growth of this industry.
In aerospace and defense, the electrical systems in aircrafts use permanent magnets to generate power. These magnets are also used in military weapons systems and in radar systems. It is therefore of both strategic and commercial interest to ensure the indigenous production of these magnets and also evaluate the current political situation and players in this industry.
The use of Nd in NdFeB magnets has grown into a large global market led by China, who accounts for more than 90% market share. The value addition along the RE production chain for permanent magnets is considerable in going from the separated oxides to the NdFeB Magnet powder with more than a $300/kg value addition.
Another recent trend is the large demand for the commercial use of Dysprosium, which is being driven by the addition of Dysprosium to NdFeB magnets.
China and Japan account for more than 90% of the global NdFeB magnet production with some production in Europe, USA and Canada. The European producers and manufacturers of NdFeB are in Germany, the UK and France. A quick analysis of Neo Performance Materials indicates that they have production facilities in China amongst other Asian countries primarily for access to raw materials. Japan as well requires a continuous supply of rare earths from China, importing 82% of their rare earths from China.
It is evident that, with the exception of China, countries that have the raw materials required to manufacture permanent magnets either do not produce them or are not major contenders in the industry. This disparity is a result of the complex patent web surrounding the invention of bonded and sintered NdFeB magnets. With numerous patents and disputes on these patents going on till date, over the composition and production process of NdFeB, the development of new technology and the entry of new players is a challenge.
For instance, two separate inventions were created, bonded and sintered NdFeB magnets with the former patent lying with USA and the latter with Japan. Japan held a strong position in the industry and licensed out its technology to China which started the development of NdFeB magnets as well. However, soon, some Chinese companies began challenging the patents held by Hitachi Metals (the successor of Sumitomo Special Metals). This is just one instance of a series of back and forth law-suits over patent infringement, market manipulation amongst a series of accusation and claims.
China’s strong position in the rare earth industry can be attributed to an early development of their national strategy for rare earth production. China has been developing industries along the RE supply chain resulting in a high domestic demand for mined rare earths. The domestic demand for the mined RE has historically been greater in China than in the rest of the world creating both a strong internal demand and an alternative economic strategy of valorization.
This new strategy is derived from China’s ‘technology for resources’ strategy whereby foreign companies are encouraged to invest in downstream rare earth processing in China. Foreign companies are not allowed to smelt or separate rare earths without a domestic partner. This push encourages companies to move their production facilities to China and transfer technology to Chinese partners in exchange for cheaper raw materials.
Although China has a large production capacity for NdFeB and exported 29,907 tonnes of the alloy as of 2017, it also imported 2357 tonnes of the alloy in the same year. The disparity between export and import prices ($49.1/kg / $91.00/kg) highlights China’s dependence on Japan for the supply of high-grade NdFeB for industries that require the use of permanent magnets in elevated temperatures and/or strong demagnetization fields.
China’s approach includes establishing joint ventures and other deals with rare earth mining companies in other countries including Vietnam, Kazakhstan, India, Namibia, Australia and Mongolia. This is one amongst multiple strategies including recycling of rare earth metals and developing alternative materials. The expenditure for all of this is through a $1.25 billion governmental policy.
India
India falls into the category of a low-cost raw materials provider. IREL supplies monazite to Japan without carrying out any valorization activities. A question arises as to how India could develop this relationship and obtain Japanese technology, and at the same time valorize monazite and increase profit margins. To understand this, we must go back to why China imports Japanese magnets when they have such a large production capacity of NdFeB magnets within the country. The reason behind this is the same as one of the reasons behind which Japan finds Indian monazite lucrative – dysprosium. Although monazite does contain numerous rare earths, Japan’s strategic position as a manufacturer of NdFeB and importer of raw materials makes dysprosium one of the most valuable rare earths for them.
Dysprosium is the key difference between low-grade NdFeB and high-grade NdFeB. With the development of new industries, the demand for high-grade NdFeB is going up and from Chinese import prices of the same, it is evident that the value added in creating these magnets is far greater than the same for lower grades of NdFeB magnets.
The addition of dysprosium allows NdFeB magnets to retain their magnetism at much higher temperatures, making them more resilient. It allows them to withstand higher demagnetization fields. Both of these capabilities make NdFeB with added Dysprosium more valuable for some industrial applications. India can realize an economic benefit by separating dysprosium from monazite and supplying high purity Dysprosium.
Dysprosium, as of July 2017 does not appear to be separated out by Indian rare Earths Limited (IREL) on a large scale. There is a supply of dysprosium Oxide to BARC for research purposes, but it is not fully commercialized. It is possible that this is due to the low concentration of dysprosium in Monazite. India is not involved in the production of NdFeB or permanent magnets from this alloy.
Furthermore, India’s current capabilities is limited to the extraction of Nd. However by adopting a similar strategy to China’s ‘Technology for Resources’ India could obtain Japan’s expertise in producing NdFeB magnets in return for a supply of raw materials rather than merely selling monazite ore to them. Domestic R&D efforts in the production of Nd magnets is also limited and could create a potential avenue for establishing an independence from foreign technology. The high value addition, market and India’s large reserves of raw materials makes R&D in this space a highly valuable venture.
India’s R&D efforts in permanent magnets so far have been concentrated on Samarium-Cobalt magnets, the predecessor to NdFeB. Samarium-Cobalt magnets retain flux and coercivity at high temperatures making them desirable for space, ballistic programs and other strategic uses.
However, the drawback of using Sm-Co magnets is the maximum energy product which is a measure of the strength of a magnet. NdFeB magnets are generally about twice as strong as Sm-Co magnets. However, the reduction in maximum energy product with the addition of Dysprosium to NdFeB magnets compensates for this disparity. The only remaining difference is in the price, with NdFeB costing $1.40/BHmax compared to $6.00/BHmax for Samarium Cobalt.
Although Sm-Co magnets can contribute greatly to solving the strategic problem around foreign reliance of permanent magnets, it does not solve the loss of an economic and strategic advantage of producing permanent magnets domestically. Unless there is extensive research done into reducing the production cost of Sm-Co or into producing NdFeB, India will continue to remain as an underutilised store of resources rather than a manufacturer in the global economy.
India has made considerable progress in the Sm-Co permanent magnet value chain. Since 2014, India has been extracting Samarium and it is likely that both the extraction and utilization of this rare earth metal is going to increase in India over the coming years.
The extraction and separation of Samarium in India coincided with the development of technology by BARC to manufacture Sm-Co magnets. As of 2018, IREL has a project underway to set up a 3000kg Sm-Co permanent magnet manufacturing facility, making valuable use of the entire RE supply chain.
Other RE Intermediates
Apart from the permanent magnets there are other RE intermediates which require an in-depth investigation. In India multiple RE metals are being underutilized both strategically and economically. The development of a strategy requires insight into the broader industries that encompass this underutilized segment of RE metals.
Phosphors are substances that exhibit luminescence and this property makes these substances viable for use in certain types of diodes and screens. The form of luminescence can vary from electro-luminescence found in LEDs where electrical current is used to produce light to fluorescence where light is absorbed and then emitted; which is useful in screens or radioluminescence where ionizing radiation is used to produce light, useful in detectors – X-ray, neutron etc.
Laser rangefinders, LIDAR, laser illuminators for reconnaissance, laser weapons are some of many strategic uses of lasers in the military. There are many different types of lasers depending on the state of the lasing medium – crystals, glasses, liquids, gases, semi-conductors. Semi-conductor lasers are typically found in CD/DVD optical pickups and in laser printers. Solid state lasers are the most significant to this report because the crystals that are used as the lasing medium are typically rare earth garnets. The most widespread crystal used in solid state lasers is Neodimium doped Yttrium Aluminium Garnet (Nd:YAG). The most common glass is Nd:glass and Y:glass. These are used to obtain very high energy outputs and find use in Nuclear Fusion research to obtain extremely high pressures required for inertial confinement and these lasers have also been used in weapon systems. They are also used for manufacturing applications like welding and cutting, in medicine and dentistry and are finding recent use as in laser igniters and certain types of spectroscopy.
With a growing share of solid – state lasers in 2017 and an expected growth in 2018, it’s important to investigate the state of this large commercially and strategically important industry in India.
Lasers in India: The broken link between industry and research
India has a 5% share of the global laser market with a history that dates back to 1992 when the first Indian laser manufacturer Saharjanand Ltd. set up their factory to build laser systems for the diamond cutting industry. In recent years, India has developed laser weapons and the DRDO has already tested a 1kW laser weapon system mounted on a truck.
A quick look at both these developments will highlight a major common theme – India imports the lasing crystals, with the tested DRDO laser weapons system being an import from Germany. Although India has many commercial manufacturers of lasers, India still does not grow the crystals in-house for commercial and military purposes.
R&D in India in lasers is quite developed with strong efforts from the Solid State Physics Laboratory in the DRDO, BARC, IISc, Raja Ramana Centre for Advanced Technology, DSC and IITK. All of these facilities have been able to grow Nd:YAG crystals in-house (amongst other crystals) and develop laser systems from these crystal rods. BARC has also developed Nd:glass lasers. The primary use of these have been for in-house research into fibre-optic communications, spectroscopic systems, laser range finders and in plasma science. This broad base of research covers numerous functionalities of solid-state lasers in both the commercial and strategic realm. The capability of numerous research institutions in India to develop laser systems hints at some collaboration between them, yet this appears to be limited to small-scale development efforts.
It’s imperative to understand if a feasibility study into the processes employed in the laboratories to grow these crystals has been conducted. This would give an indication of the major roadblocks the industry is facing. Considering how the development of lasers and laser crystals have successfully taken place within the laboratories of the DRDO, it’s odd that the DRDO would still rely on imports from Germany. This could perhaps indicate that the technology in India is still behind global competitors either from a cost or from a utility standpoint.
It is necessary to shift the production of crystals in-house and encourage both governmental and private groups to do so. This would establish a loop that would push R&D efforts in this space for the entity producing laser crystals to remain relevant and competitive and this R&D would also be effectively implemented in industry. An initial push could be strategic, to make India’s laser weapons program covert by stopping imports, which would eventually trickle into the private sector as well.
Nuclear Energy
Several rare earth elements can absorb thermal neutrons and have large capture cross sections. They are therefore useful for controlling nuclear reactions and are used in control rods. Europium and Dysprosium are predominantly used as they absorb a large number of neutrons per atom (4 and 2.4 respectively), however, Samarium and Gadolinium which absorb 0.4 and 0.3 neutrons per atom can also be used.
Dysprosium Titanate is an attractive control rod material and has been used in the VVER-1000 since 1995. The VVER reactors at KudanKulam which have been set up in collaboration with the Russian Federation also utilise Dysprosium Titanate in their control rods. As a part of the deal between the two countries, Russia will supply equipment, material, fuel and machinery and therefore indigenous capabilities are not revealed.
However, looking into research it is evident that India has done extensive research into dysprosium titanate as an absorber in control rods. This has been done with indigenously sourced dysprosium oxide, indicating valuable strides on both fronts – nuclear strategy as well as the indigenous utilisation of rare earth elements.
Gadolinium oxide is the other substance that can be used in control rods. Although they are not as efficient in neutron absorption, they have been used in various nuclear reactors. India’s first nuclear plant, the TAPS uses Gadolinium as burnable poison rods. Gadolinium oxide is added to Uranium Oxide to make pellets that are used in the fuel bundles of TAPS. This is regularly manufactured by the Nuclear Fuel Complex in Hyderabad, India.
A paper from the Nuclear Fuel Complex indicates that there is more than one potential supplier of gadolinium Oxide. Further, it highlights the necessity for high quality (density, geometric integrity and microstructure) of raw materials in manufacturing pellets for the PHWRs. The challenge therefore lies in producing high quality rare earth oxides indigenously and through collaboration between different institutions in India, and this can be achieved.
Conclusion
Earlier studies have highlighted various issues in setting up a RE industry in India despite the country possessing vast RE resources. Of these, the most notable problems were the lack of major links between research and industry as well as the lack of a national strategy with regards to the rare earths value chain. As seen in this report, predominantly through the development of separation facilities and the Samarium Cobalt plant in IREL, it becomes evident that steps are being taken towards developing India’s position in the rare earths market. The collaboration between BARC and IREL to develop the Sm-Co plant demonstrates a concrete link between a research institute and an industrial entity, providing both an economic and strategic benefit. Some of these recent developments are in the right direction whereas others could be leveraged better. The sale of Monazite to Japan at a time when Japan is trying to diversify its rare earth resource base might be a strategically undervalued approach. Although, if this sale of non-valorised products is benefited by a valuable technological exchange, it might allow the future realisation of value. The lack of development of other rare earth value chains for both strategic and commercial purposes has also been highlighted. Notably, the lasers industry appears to be a logical next step as the research to grow garnets from rare earths has existed for a while and only the indigenous implementation of this research in industry must take place. With regards to permanent magnets, the report reasons why India must continue to push to develop Nd-B-Fe magnets or develop technology to reduce the cost of producing Sm-Co magnets. Finally, the requirement of high quality raw materials for nuclear purposes highlights the necessity to develop better facilities and technology to be used in the earlier stages of extraction and separation of rare earths by IREL.